Alumina
-
Alumina Basics
What is alumina?
Alumina is aluminium oxide (Al2O3) and is usually produced as a white crystalline powder.
Over 94% of all alumina is used to produce primary aluminium metal in electrolytic aluminium smelters. The remaining alumina is used in a variety of other applications including refractories, abrasives, chemicals, fillers and even cosmetics.
Source: Hydro Photo Rosangela Aguiar
In 1887 Carl Josef Bayer invented the ‘Bayer process’ which still today is the mainstay of alumina production. The Bayer process uses concentrated caustic solutions (liquor) to dissolve naturally occurring aluminium hydroxy-oxides (Al2O3.H2O or Al2O3.3H2O) from bauxites and then re-precipitate them as nearly pure aluminium tri-hydroxy-oxide (Al2O3.3H2O known ‘hydrate’ or ‘tri-hydrate’). The tri-hydrate is then heated (‘calcined’) to ~1000°C to remove the chemically bound water, leaving highly purified Al2O3.
The almost synchronous developments of the Hall-Héroult process for primary aluminium smelting in 1886 and the Bayer process in 1887 enabled the modern aluminium industry; taking aluminium from being a rare and expensive metal to its current commodity status.
Production & Trade
Approximately over 130 million tonnes of alumina (chemical and metallurgical grade) was produced in 2019, with 2019 world capacity at this time estimated at 153 MTPY.
China is the largest producer. Producing over 70 million tonnes in 2019, accounting for 54% of the world total. Australia, ranked a distant second with over 20 million tonnes and the third largest producing region was South America with over 10 million tonnes. Together, these three regions make up 77% of the worlds production. In the past decade, China had consolidated its dominant position as the #1 producer with steadily growing capacity – in 2014, China’s total refining capacity accounted for over half of the world total for the first time, and its proportion has been increasing, to 58% in 2019. China, turned a net export of alumina briefly in 2018, and then has re-instated as a net importer.
Australia’s alumina production has been stable and is forecast to remain so for the next few years, at over 20 million tonnes. In 2018, nearly 18 million tonnes or 88% of its alumina produced were exported.
-
Types of Alumina
There are several different types of alumina:
- Smelter Grade Alumina (SGA) or metallurgical grade alumina – used for the production of primary aluminium metal
- Refractory grade alumina’s – of varying purities, used in the production of refractory products and abrasives.
- High Purity Alumina (HPA) – used for alumina chemicals, advanced refractories, cosmetics etc.
Additionally un-calcined hydrate (Al2O3.3H2O) is often sold directly to chemical and high purity applications where is further refined or processed.
-
How is Alumina Produced?
Production processes
The goal of refining is to isolate and retain only the aluminium hydroxy-oxides (Al2O3.H2O or Al2O3.3H2O) from bauxite and let the impurities (principally iron oxides and silica minerals) pass from the process. The outputs of the refining process are alumina tri-hydrate and a ‘red mud’ waste stream containing the impurities. The alumina tri-hydrate is then calcined at ~1000°C to drive off the water, leaving alumina at typically >99.5% purity.
-
How is Alumina Produced? - Sinter
Sinter
Once a mainstay of the Chinese alumina industry, and alumina production in the former Soviet block countries, the sinter route takes a pyro metallurgical approach to ‘lock-up’ the silica and thus prevent it from contaminating the product alumina. The process is significantly more costly, both capital and operating costs, thus most sinter plants have closed. It has the advantage of being able to treat very low ratio alumina to silica ratio bauxites (low A/S bauxites) and in its ability to produce a higher purity product (thus making it better for lower volume applications demanding higher purity or higher whiteness).
Another drawback to the sintering technology has been that in its traditional form the alumina produced is very fin grained, making it more difficult to handle in modern smelting equipment.
- Comminution: bauxite is ground with limestone and sodium carbonate or caustic.
- Sintering: The ground meal is charged to a large rotary calciner, typically fueled by coal or oil and heated to ~1200°C. The silicate minerals react with the calcium in the limestone to form dicalcium silicate (Ca2SiO4) rendering far less soluble in the later hydrometallurgical stages. Alumina forms the highly soluble sodium aluminates.
- Clinker cooling and grinding: the clinker from the sinter operation is cooled and ground.
- Leaching: The ground clinker is leached using sodium carbonate solution.
- Clarification: The pregnant liquor is separated from the clinker grinds
- De-silication: The pregnant liquor is heated and held to precipitate any silica picked up during the leaching stage.
- Clarification: The liquor is again clarified to remove any solids that would give silica carryover to the final product.
- Precipitation: The pregnant liquor is forced to precipitate tri-hydrate by injecting carbon dioxide (captured from the off gas of the sintering operation). The tri-hydrate is very fine grained. The material is also washed to ensure minimal liquor carryover to the hydrate material.
- Calcination: The alumina tri-hydrate (Al2O3.3H2O) is calcined at ~1000°C to drive off all chemically bound water, to leave alumina typically >99% Al2O3.
-
How is Alumina Produced? - Bayer
Bayer
Today the Bayer process dominates the production of alumina as it is the lowest cost production route. The process uses a recirculating volume of concentrated caustic solution to dissolve the alumina minerals, separate them from still solid impurities, and then re-precipitate alumina tri-hydrate. Calcining completes transforms the tri-hydrate to alumina.
- Comminution: Incoming bauxite is ground to a smaller particle size to enable faster digestion and mixed with highly caustic liquor.
- Pre-desilication: The slurry is sent to pre-desilication stage (~100°C, atmospheric pressure). This helps to pre react any clays or other highly reactive silica containing minerals in the bauxite and start the formation of de-silication product (DSP). Pre-desilication minimises the residence time of the slurry in the more expensive hot digestion stages.
- Digestion: The pre-desilicated slurry is sent to the digestion process. Here the slurry is heated to between ~140°C and 260°C (depending on the type of bauxite – see the “Bauxite 101” section of this website). The alumina and silica minerals dissolve and then the silica re-precipitates as ‘desilication product’ (DSP). The DSP contains caustic, alumina and silica roughly in the mass ratio of: 1:1.25:1.5. Thus the removal of silica also causes valuable caustic and alumina to report to the waste stream.
- Flash down: The heated slurry is cooled to 105°C (and the pressure reduced back to atmospheric) by allowing steam evaporation or flashing in a cascade of vessels. DSP formation should be completed in this stage, however the bulk of the alumina minerals remained dissolved in the liquor.
- Separation & clarification: The solid and liquid components of the slurry are separated using cascade of settlers or deep cone separators to recover as much of the entrained liquor as possible. The high solids content mud is sent to permanent disposal site. The pregnant liquor and washings are sent to filtration or polishing to remove virtually every trace of solids content – helping avoid impurity contamination of the final product and preventing nuclei carryover to the precipitation process.
- Precipitation: The pregnant liquor is gradually cooled from approximately 80°C to 65°C in a cascade of large vessels. The dissolved alumina precipitates as alumina tri-hydrate (Al2O3.3H2O). The alumina is hot washed to remove oxalates which also precipitate out of the liquor. The spent liquor.
- Calcination: The alumina tri-hydrate (Al2O3.3H2O) is calcined at ~1000°C to drive off all chemically bound water, to leave alumina typically >99.5% Al2O3.
- Other: Streams of the spent liquor are now further treated to remove other impurities, partially evaporated to remove excess water, and used to preheat incoming slurry (to save on process energy costs). Additional caustic is added to make up for losses to the red mud stream.
Sweetening
In Bayer refining of high temperature bauxites (typically those bauxites requiring a digestion temperature of 250 °C or greater), there is a process variant know as sweetening. It involves injecting an extra ~25% of low temperature (gibbsitic) bauxite slurry into the flash down (Stage 4 ). The alumina in the gibbsitic bauxite slurry dissolves rapidly in the high temperature stream, allowing the concentration of dissolved alumina in the liquor to be significantly higher than could otherwise be achieved by processing high temperature bauxite alone. In this way “sweetening” allows extra alumina to be produced from an existing high temperature plant for only a very small capital and operating cost increase (pro rata, far less than the alumina produced).
-
How is Alumina Produced? - Combination
There have been a number of attempts to combine Bayer and Sinter technologies in an effort to find an economic means of processing low grade bauxite. To date none of these has really proved that successful and all bar some plants in China and one in Kazakhstan have closed.
The one combination variant that does stand a chance of success, in a low cost country such as China, is the Red Mud Sinter (RMS). In this variant the mud from the Bayer plant is sintered allowing the reclamation of most of the caustic soda and alumina that would otherwise be lost to the red mud. To be successful the cost of energy and interest on capital for the extra plant required must be less than the cost of lost alumina and caustic that would otherwise occur.
-
How is Alumina Produced? - Other
There are a number of other routes for producing alumina that have been practiced or investigated over the decades, however none of these have been viable outside controlled economies of the past. Alumina containing inputs to these processes can include bauxite, but are more typically other lower cost materials such a aluminous clays, high alumina fly ash, or in the case of a former Soviet plant, nepheline.
Very often these non-Bayer processes would rely on the sales of by-products such as cement or zeolites to be economic.
Acid routes
Processing bauxites or other alumina containing minerals with acids has been experimented with extensively. No large scale commercial plants have ever been constructed due to higher operating and capital costs. Additionally corrosion problems and potential leaks of toxic reagents (eg chlorine gas) add to potential operating difficulties. The acid routes, due to their ability to produce a very high purity alumina in a single process, do have potential for the production of small quantities of high purity alumina for specialised applications (but not SGA).
Greymeck
The Greymeck process once operated in Poland is essentially a wet cement process that also produces alumina; it produces around 9 tonnes of cement for every tonne of alumina. Based around sinter technology, one plant in China (Mengxi) has been built around this technology. The aluminous feed stock for the process is high alumina fly ash.
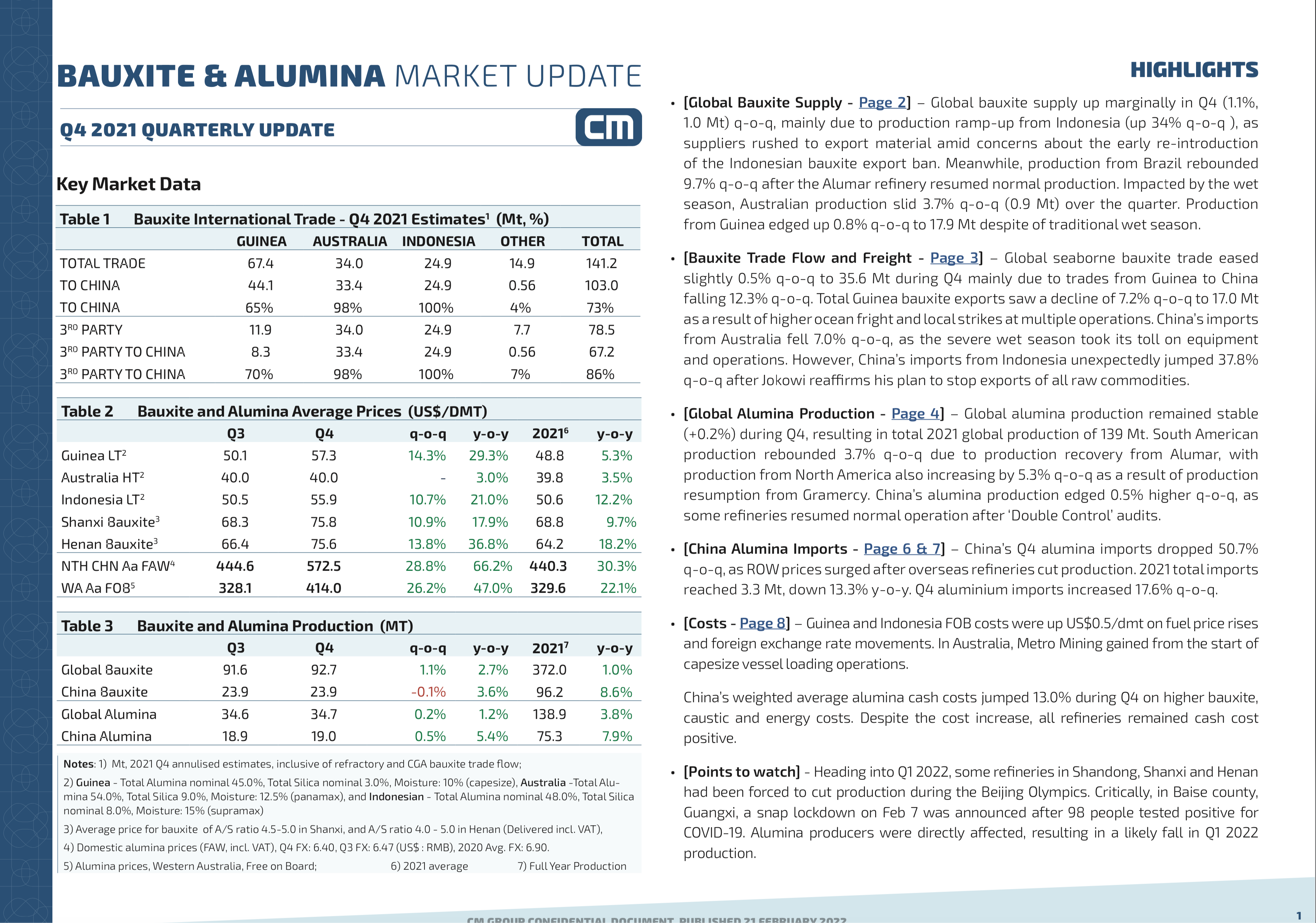
Bauxite Index Quarterly Wraps
Get started with a subscription today.
China’s Aluminium Value Chain Quarterly Update is an independent and detailed assessment of the key metrics of China’s bauxite, alumina and primary aluminium industries, as we see them, presented in the form of an easily digestible set of charts and tables, together with relevant commentary on significant events, emerging trends and other key themes arising from our analysis.
For over a decade, we have been continually conducting in-depth studies of these industries in China, among which field studies are a cornerstone of our work. Over that time, we have drawn on, and continue to draw on, a diverse range of sources to gather primary data, on which our analyses and forecasts are based.
Access Now